FedEx and UPS had the same GRI for 2024 at 5.9%. Down 1% from 2023’s 6.9% increase.
American businesses are facing shipping cost hikes that are significantly higher than what these published rates suggest.
Let that sink in.
Despite the sharp increase in shipping costs, this fragile supply chain model of not diversifying carriers has a darker side. Imagine a world where a single glitch in your supply chain can halt your entire business operation. This is not just a hypothetical scenario; it’s a reality many businesses faced during the COVID-19 pandemic. The disruptions highlighted the frail nature of supply chains dependent on a single carrier. This brings us to a crucial question: How can businesses build more resilient supply chains?
Carrier diversification.
But how exactly does this work? What kind of monitoring and operations are involved? Why is it so significant in today’s logistics industry? What’s changed in the market? What are the challenges involved?
Let’s dive into it.
The post-COVID era has exposed vulnerabilities and underscored the need for new strategies to ensure supply chain resilience. Since Covid, shippers have faced many complex problems with FedEx and UPS. Both of these companies have had a strong duopoly over global supply chains until now. Unfortunately, we’ve not had a direct replacement for these carriers, leading to the never-ending rate increase saga between the two companies.
Carrier diversification can put a stop to the problems mentioned above and comes with several benefits, such as:
- Risk reduction: By partnering with multiple carriers, you reduce your reliance on a single carrier.
- Cost savings: Through balancing discount tiers and finding favorable rates for specific services.
- Lowered transit times: By leveraging direct shipping routes and minimizing unnecessary stops.
So, what metrics should you look into before diversifying your carriers?
How do you identify an excellent distribution network and a not-so-great distribution network?
How can you reduce your average cost per zone, average cost per pack and/or transit days?
How do you bring down your accessorial charges?
Every single year, we see freight charges go up by 6-7%, but accessorial charges go up significantly higher. It’s increased by 20% yearly for the past three or four years (since COVID hit). The oversize accessorial charges have gone up by a staggering 250%. Overmax (UPS oversize charges) has increased by 1500% in the last 5-6 years. When you look at it, it’s not even viable to ship heavier packages via FedEx and UPS anymore.
Let’s look at some examples and answer the above questions.
Understanding and Implementing Carrier Diversification: Explained with Example
Below is a snapshot of a shipper’s Spend Trend Summary. This dashboard gives you the exact figures for total shipping spend and accessorial spend.
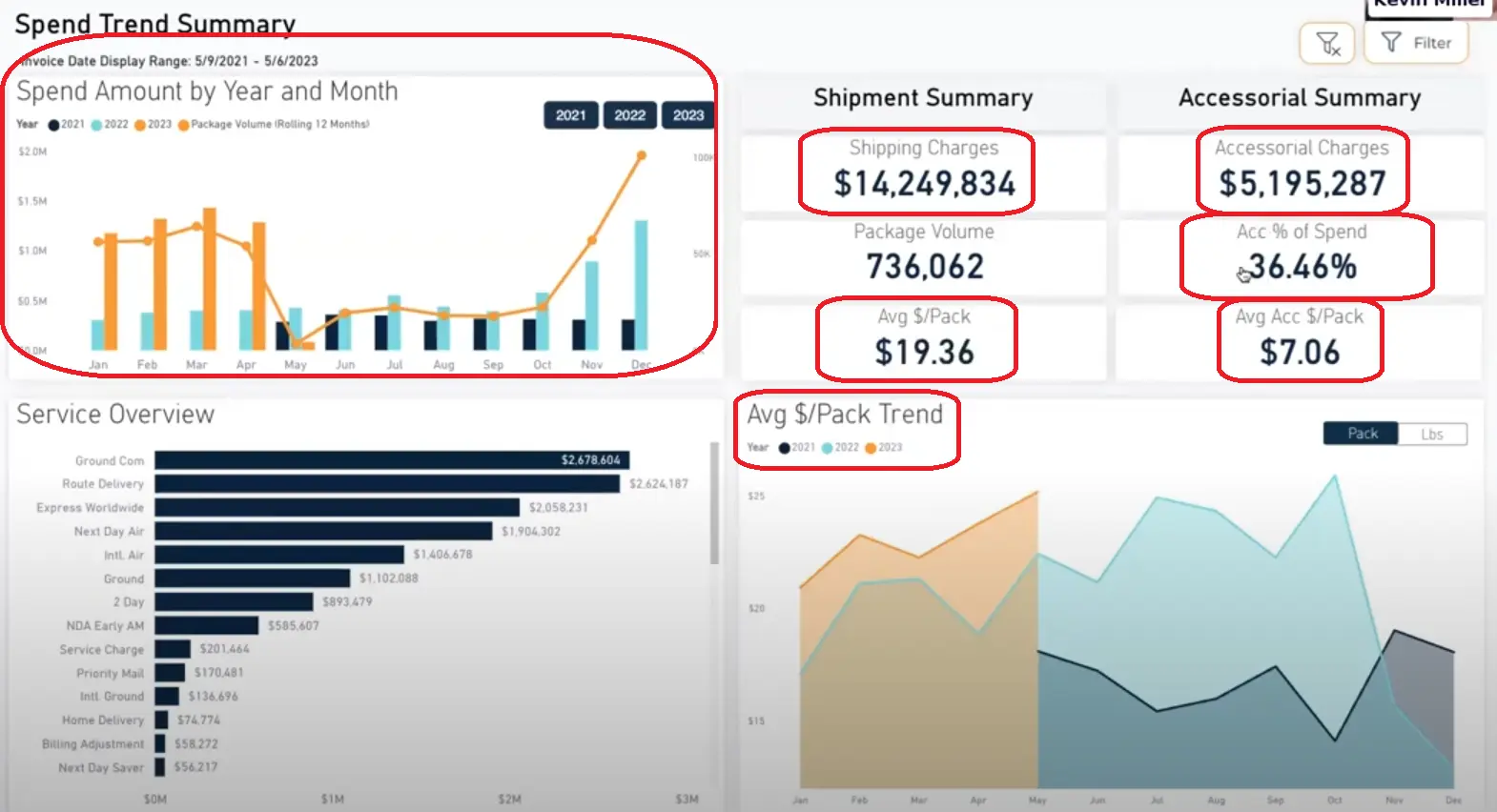
Spend Amount by Year and Month
Trend Analysis: The graph shows the spend amount from 2021 to 2023, with a noticeable increase in spending in 2023. A significant spike is observed in the later months of 2023, indicating two things: Higher shipping costs or increased shipping volume during this period. If your shipping volume numbers didn’t change significantly, it implies that your shipping costs have gone up. And what can we do about it? Let’s break down the Spend Trend Summary and analyze further.
Shipment Summary with Key Performance Indicators
The shipment summary is broken down into three KPIs, namely:
- Shipping Charges: The total shipping charges amount to $14,249,834
- Package Volume: The volume of packages shipped is 736,062
- Average Cost per Package: The average cost per package is $19.36
Accessorial Summary: Find Out What’s Inflating Your Costs
In general, for industries with few oversized packages or residential deliveries, the accessorial spend range of 20-25% is what we consider to be healthy. However, here, we see that it’s 36.46% of the total spend and should be looked into further to bring it down a notch. That said, every industry is different. If you’re mostly shipping heavy packages, expect this KPI to be higher than average.
- Accessorial Charges are additional fees applied to base shipment costs imposed by carriers for services beyond the standard transportation of goods. Common accessorial charges include fuel surcharges, hazardous material handling fees, holiday or weekend delivery charges, etc. Here, they sum up to $5,195,287.
- Percentage of Spend: Accessorial charges represent 36.46% of the total spend
- Average Accessorial Cost per Package: The average accessorial cost per package is $7.06
Average Cost per Package Trend
Yearly Comparison: The trend analysis shows the average cost per package from 2021 to 2023, with an upward trend indicating increasing costs. This is where we can look for opportunities to diversify carriers and simulate to see if we can bring down the average cost per package in the coming years. How? You can do this by classifying your spend based on service types. This is where ‘Service Overview’ comes in handy.
Service Overview: Identify Your Shipping Expenses
Understanding where your shipping expenses are concentrated is crucial for optimizing costs. Let’s explore the top services by spend to explore savings opportunities.
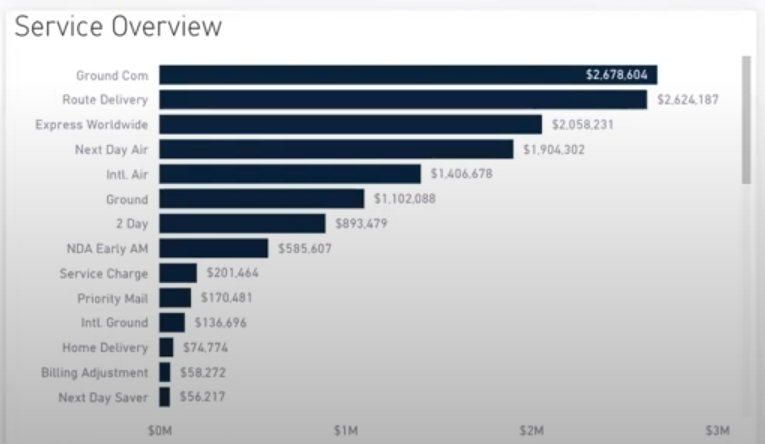
The ‘Service Overview’ section highlights the top services by spend, indicating where most shipping expenses are concentrated. Here’s an analysis of what this implies:
Ground Commercial: $2,678,604
Implication: Ground commercial shipping represents the largest portion of the shipping budget. This indicates that a significant volume of shipments is being handled via ground services, which are generally more cost-effective for domestic deliveries compared to air services. The high spend suggests a large volume of shipments or possibly higher rates.
Route Delivery: $2,624,187
Implication: Route delivery services cost nearly as much as ground commercial services, indicating that scheduled delivery routes are in high demand and frequently used. This may imply a structured and consistent delivery schedule, possibly for regular, repeat customers or businesses with fixed delivery routes.
Express Worldwide: $2,058,231
Implication: The considerable expense on express worldwide shipping shows a significant reliance on fast international deliveries. This suggests a global customer base that needs expedited shipping options, which are generally more expensive.
Next Day Air: $1,904,302
Implication: The high spend on Next Day Air services highlights a strong demand for urgent deliveries for this shipper. This service is critical for businesses that need to meet tight deadlines, indicating the importance of speed in their logistics and supply chain operations.
International Air: $1,406,678
Implication: Spending a substantial amount on international air shipping indicates a robust international shipping operation. This service is essential for quick, long-distance deliveries, reflecting the need for efficiency and speed in global logistics.
The more you understand your data, the more you understand the factors that need to be optimized.
Time in Transit: How Precision Data Helps You Optimize Your Logistics
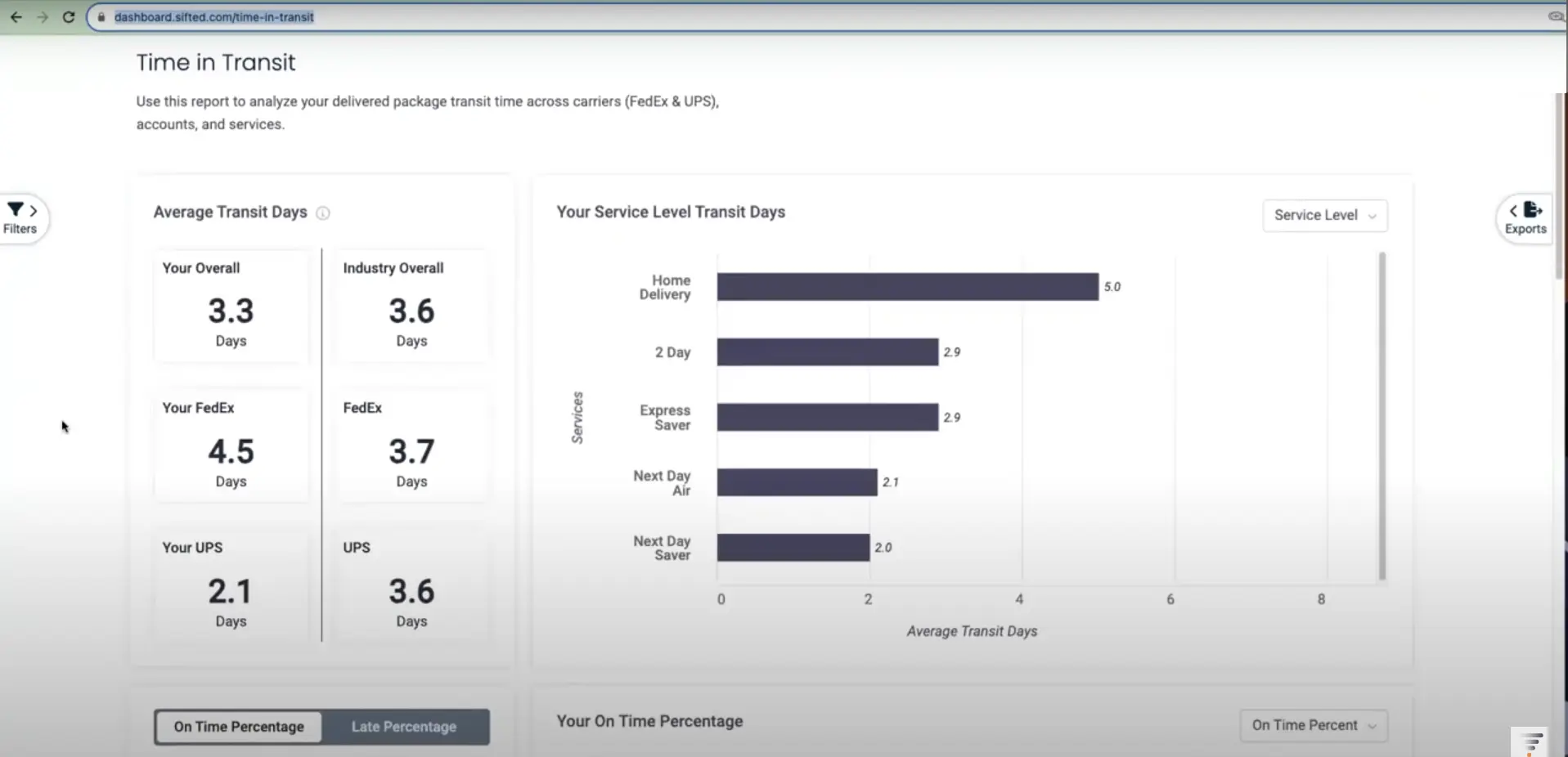
In September 2023, Sifted launched the Time in Transit dashboard, where you can compare your transit times against industry standards.
Let’s take a look at the example above. The shipper’s average transit days via FedEx is 4.5 days, whereas, the industry average is 3.7 days. So there’s a gap that indicates carrier diversification might make sense here.
On the other hand, with UPS, the shipper’s average transit days is just 2.1 days – which is much lower than the industry average. This is a great thing to know as a shipper because you can now ship more packages faster without fighting and experimenting with your logistics operations.
That said, there can be many reasons as to why UPS has a better transit time with this shipper. They might be closer to a UPS distribution center, or using more express services. It is important to dive into the “why”.
In addition, you must also look at on-time percentages if that’s crucial to your business.
Carrier diversification weighs in a myriad of options to optimize your shipping. And that’s why having clear visibility into your data is key.
Want our software to analyze your shipping health and help reduce your shipping expenses?
Frequently Asked Questions: Carrier Diversification and Regional Carriers
1. What’s the impact of using a regional carrier outside of your region ID? For example, if you’re on the West Coast, can you use an East Coast Regional carrier?
That’s a really good question. We get asked that all the time. Let’s look at an example.
I’m on the West Coast. I’ve got a substantial amount of business on the East Coast. How can I use a regional carrier?

There are two main ways to use a regional carrier outside of working with them directly:
- Line Hauling: If you have enough volume going to one part of the United States where you don’t have a facility, you can line haul for improved efficiency. Line hauling involves consolidating a number of shipments, then sending via a freight or LTL service haul to a single destination (somewhere on the East Coast, in this example). There, it can be injected directly into a regional carrier’s network.
- Third-party warehousing: The second way to use regional carriers outside of your region is to partner with a third-party logistics provider (3PL) that is located in the regional carrier’s footprint. The 3PL will store, pick, pack, and ship products with the carrier you’re employing. By using a 3PL, you can expand your distribution network much faster than building your own distribution center.
2. Doesn’t line hauling increase the transit time?
Line hauling can actually reduce your transit times while also reducing costs. By hauling the packages cross-country before injecting them into the parcel carrier’s system it can reduce the amount of stops made along the way. Fewer stops can also lower the risk of damaged goods during transit. Regular, scheduled line haul services provide predictable and reliable delivery times, which are crucial for maintaining tight supply chain schedules.
3. Can you explain ‘Line Hauling’ in detail? What are its key characteristics?
Key Characteristics of Line Hauling:
- Long-Distance Transport: Line hauling involves the movement of goods over considerable distances, often spanning multiple states or countries.
- Efficient and Cost-Effective: By consolidating shipments into large loads, line hauling maximizes transportation efficiency and reduces costs. It takes advantage of economies of scale, making it cheaper to move large quantities of goods.
- Critical Supply Chain Segmentation: In a supply chain, line hauling connects the initial point of shipment (e.g., manufacturer or supplier) with distribution centers or major hubs. From these hubs, goods are then distributed to final destinations through shorter, more localized delivery routes.
4. What are the advantages of line hauling?
Line hauling offers several advantages that could make it a great addition to your carrier mix, if it makes sense for your business.. Here are the key benefits:
- Cost Efficiency: By transporting large quantities of goods over long distances, line hauling leverages economies of scale, reducing the cost per unit of transport. Bulk shipments typically have lower costs compared to multiple smaller shipments.
- Reduced Fuel Costs: Efficient routing and larger vehicle capacity can lead to lower fuel consumption per unit of freight, further reducing costs.
- Reduced Handling: Goods are typically handled less frequently during line haul transportation, reducing the risk of damage.
- Faster Transit Times: By moving directly between major hubs, line haul services can offer quicker transit times compared to multiple smaller shipments.
- Improved Inventory Management: By moving goods to central distribution centers, companies can better manage inventory levels, streamline warehousing operations, and quickly respond to changes in demand.
5. But 3PLs, third-party warehousing and diversifying carriers will probably increase my shipping expenses?
Third-party warehousing and 3PLs can often reduce overhead costs, lower operational costs and drive speed in your logistics processes. Here’s how:
- Reduced Overheads: Companies can avoid the significant capital expenditure associated with building and maintaining their own warehouse facilities. Instead, they pay for the space and services they need, which can be scaled up or down based on demand.
- Lower Operational Costs: Outsourcing warehousing to a third party can lower labor and operational costs, as the 3PL provider handles staffing, training, and management.
- Scalable Services: As your business grows, 3PL providers can scale their services to match increased demand without requiring the business to invest in additional infrastructure, manpower and resources needed to scale the growth.
- Easy access to shipment data: Many 3PLs use sophisticated warehouse management systems (WMS) that provide real-time inventory tracking, automated order processing, and data analytics to improve efficiency.
- Strategic Locations: 3PL providers often have a network of warehouses in strategic locations, allowing businesses to store products closer to key markets and reduce delivery times significantly. By outsourcing warehousing functions, businesses can focus more on their core activities, such as product development, marketing, and sales, rather than on logistics and warehousing issues.
6. How do carriers like FedEx and UPS run their national logistics networks?
National carriers like FedEx and UPS operate massive hubs where products are sorted and dispatched.
Consider an example of an overnight shipment with FedEx from Los Angeles, California to Salt Lake City, Utah.

FedEx is represented in orange, and a regional carrier, OnTrac, is shown in dark blue.
In this scenario,, FedEx picks up the package in Los Angeles and flies it all the way to their major sorting facility in Memphis, Tennessee. This hub is a central part of FedEx’s national network. Once the package is sorted in Memphis, it is flown back across the country to Salt Lake City.
This process, although seemingly indirect, allows FedEx to efficiently manage and route a vast number of shipments through their centralized hub system.
When a package travels this far of a distance though, there are two main concerns:
- There is more room for a potential error or mishap
- Shippers who care about their carbon footprint and sustainability don’t approve of this model
On the other hand, regional carriers, in this case OnTrac, pick up the shipment in Los Angeles, next moving it to their Reno, Nevada search facility and then finally directly over to Salt Lake City.
Let’s compare the cost difference, miles traveled and transit times between the two models:
Carrier | Average Cost Per Pack | Transit Time | Miles |
---|---|---|---|
FedEx | FedEx Overnight costs $38.11 | 1 day | 3275 miles |
OnTrac | 50.55 | 1 day | 644 miles |
In this case, OnTrac is 3x cheaper than FedEx AND travels 5x less miles – a win-win!
Looking to bring on a regional carrier and need help identifying the right carrier for you, get in touch with us here.
Our software can help you evaluate the performance of your current carrier mix and understand where adding to it might make sense.
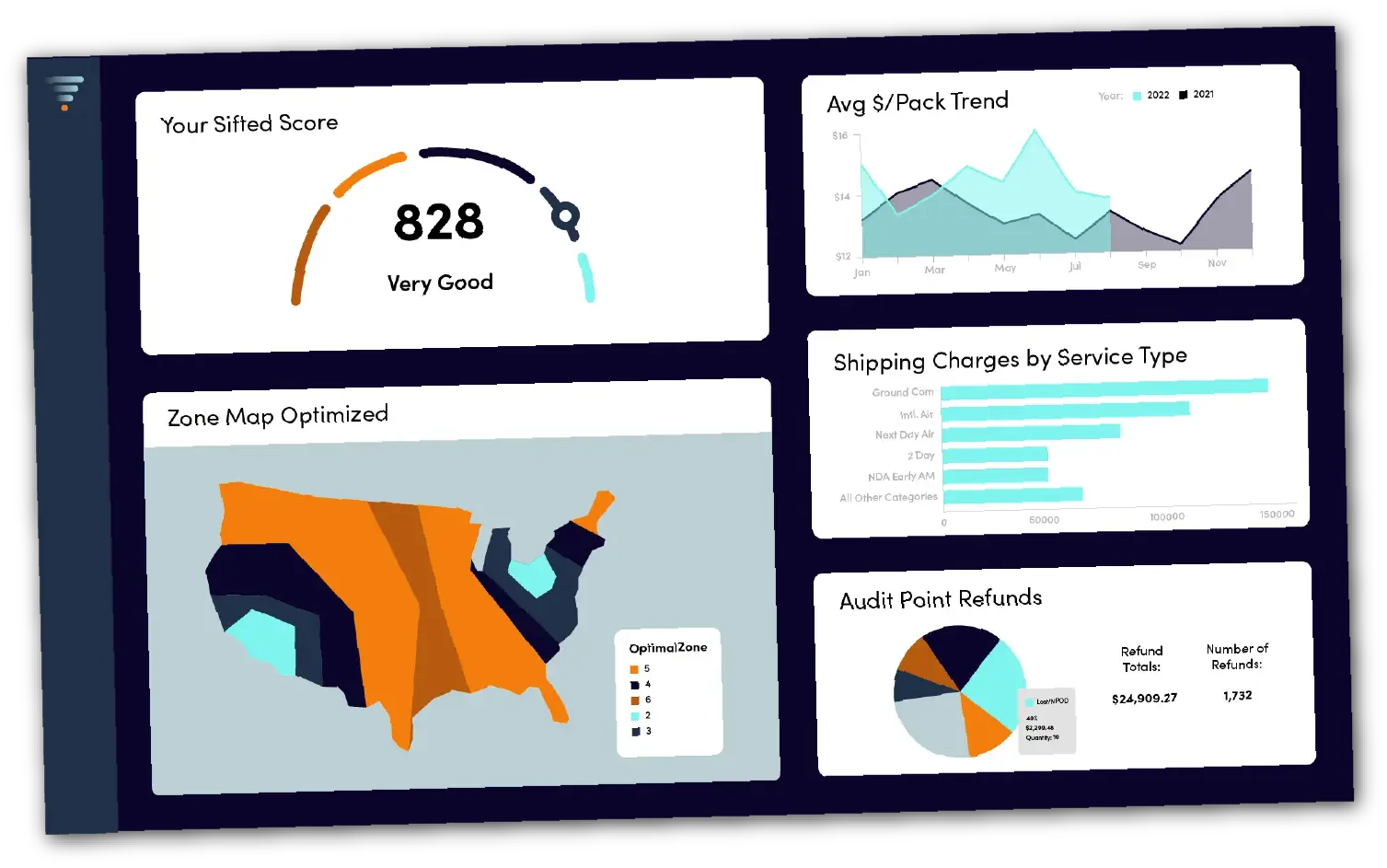
Sifted Logistics Intelligence